Troubleshooting Guide Renard 64XC
Jump to navigation
Jump to search
Introduction
- This page is intended to help identify/isolate some of the common problems individuals encounter when building/operating the Renard 64XC controller board.
- The troubleshooting procedures provided here are presented in a detailed step-by-step systematic approach. This approach is not necessarily the quickest way to find your problem. If you are looking for a quick fix, then swap anything/everything that you can and come back to these procedures if you are still having problems.
- The following procedures require the individual to be familiar with the operation of a digital multimeter (or voltmeter/ohmmeter if you prefer). If you currently do not know how to measure resistance or how to measure voltage, please take some time now an learn these basic skills before attempting these procedures. This website provides some basic information on using multi-meters. They have different types and model and even have a few videos!
All DC voltages in this document are referenced to GND. So for all measurements, the multimeter negative (-) lead, usually black, needs to be connected to a GND point on the PCB. The best location would be the GND Test Point TP1 located near RJ45 Jack J21. The positive lead (+), usually red, gets connected to the location called out in the procedure. |
Disclaimers
- Due to the nature of the information contained on this page, it is imperative that all individuals read and understand the disclaimers contained here.
Basic Troubleshooting Info
Verify Setup
- The first step to successful troubleshooting is to ensure that your setup is correct.
- Verify that the Renard board is assembled correctly as compared to the Renard 64XC Controller Assembly Instructions wiki.
- Verify that you have power/control cables connected correctly as compared to the Renard 64XC Controller wiki.
- Verify that you have the Vixen plug-in settings correct as compared to the Renard 64XC Controller wiki.
Most Common Problems
- These are the most common problems encountered by individuals who have built Renard boards since their debut to the DIYC community:
- Missed solder pads or bad solder joints. Many individuals get in a rush when assembling their boards and will occasionally miss a solder pad or just do a poor job on a particular solder pad. This type of problem can usually be easily identified by closely inspecting all the solder pads on the board after assembly is complete. Missed solder pads may/will cause many different problems that will cause you to spend many hours troubleshooting only to find that it was as simple as a missed solder pad. So take your time and closely inspect your solder work when you are done with the assembly. It is strongly suggested that you inspect the joints with a good magnifying glass under really good lighting.
- Bad data cable coming from the computer. Many individuals assume that all serial cables are identical, but that is far from the truth. Just because a cable has the correct DE9 connectors on each end doesn’t mean that the wires inside are going to the correct pins for Renard operation. It is always best to physically check the pin continuity to verify that the cable will work for Renard operation. Make sure that your interconnect cable is wired according to the Renard 64XC Controller wiki.
- PICs with corrupted firmware or no firmware. This mostly affects individuals who get their PICs from a “group buy” with the firmware already loaded but also does impact those who program their own PICs. For whatever reason, sometimes a PIC (believed to be correctly programmed) will not behave correctly and needs to be re-flashed with the firmware. Once it is re-flashed, it then works correctly. This is why all individuals who are using these boards should invest in a PIC programmer. A programmer will also enable you to switch to the diagnostics firmware, which will help tremendously during troubleshooting. Your best bet is to get the PICKIT2 or PICKIT3 from Microchip.
- Incorrect Vixen Settings. It cannot be emphasized enough, the Renard boards will not work correctly if Vixen is not setup correctly. Verify that you have the Vixen plug-in settings correct as compared to the Renard 64XC Controller wiki. The settings in Vixen must match the setting used in the Renard Firmware burned onto the PICs.
Troubleshooting the Renard 64XC Controller
Troubleshooting Flow
The complete pdf version of this flowchart can be found here
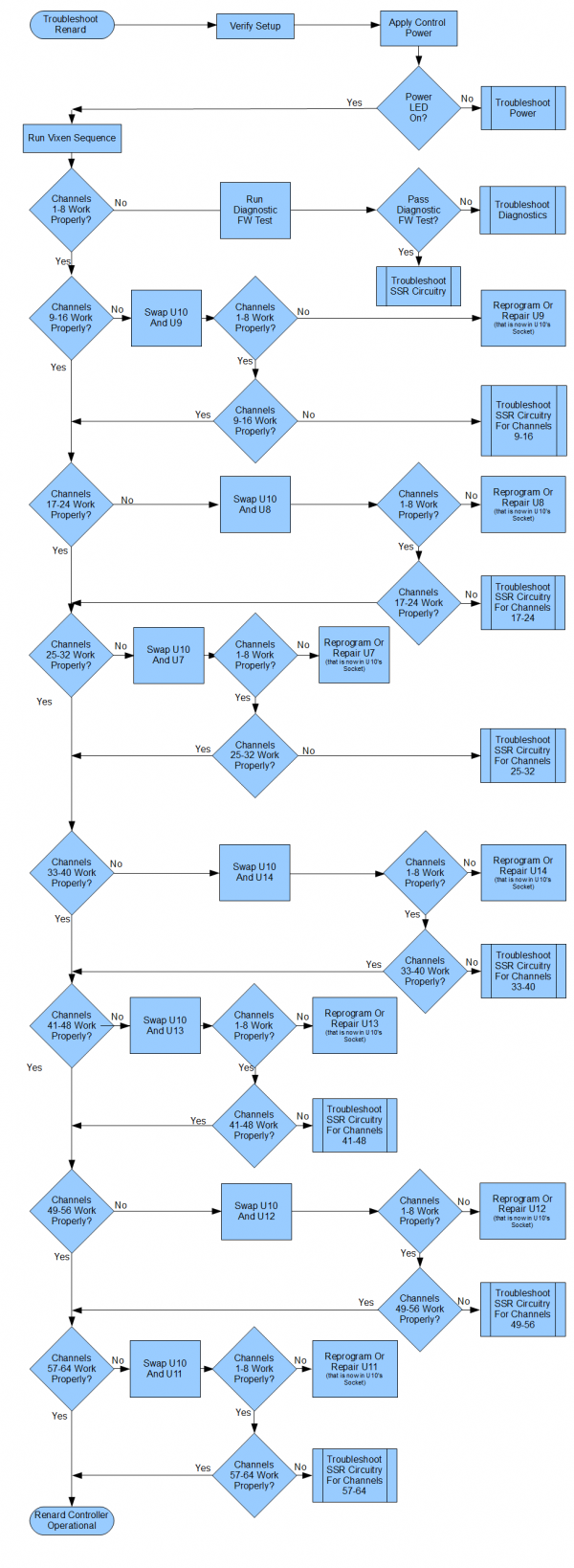
Troubleshooting Steps
- Verify that you have the power/control cables connected correctly as compared to the Renard 64XC Controller wiki.
- Verify that you have the Vixen plug-in settings correct as compared to the Renard 64XC Controller wiki.
- For the following steps, the PICs (U7 thru U14) need to be programmed with the Renard Operational Firmware.
- Turn ON AC power
- PWR LED should be lit
- If incorrect , then go to Troubleshooting Power Problems.
- Run a Vixen sequence
- Do Channels 1 thru 8 respond as programmed in the Vixen sequence?
- If they don't, then go to Troubleshooting Diagnostics Problems.
- If the diagnostic routine passed, then go to Troubleshooting SSR Circuitry Problems.
- Do Channels 9 thru 16 respond as programmed in the Vixen sequence?
- If they do, go to step 15
- Turn OFF AC power
- Swap PIC chips U10 and U9
- Turn ON AC power
- Run the Vixen sequence again
- Do Channels 1 thru 8 respond as programmed in the Vixen sequence?
- If they don't, reprogram or replace the U9 PIC chip that you moved to the U10 socket and retest
- Do Channels 9 thru 16 respond as programmed in the Vixen sequence?
- If they don’t, then go to Troubleshooting SSR Circuitry Problems.
- Do Channels 17 thru 24 respond as programmed in the Vixen sequence?
- If they do, then goto step 22.
- Turn OFF AC power
- Swap PIC chips U10 and U8
- Turn ON AC power
- Run the Vixen sequence again
- Do Channels 1 thru 8 respond as programmed in the Vixen sequence?
- If they don't, reprogram or replace the U8 PIC chip that you moved to the U10 socket and retest
- Do Channels 17 thru 24 respond as programmed in the Vixen sequence?
- If they do, then your Renard SS24 Controller board is operational
- If they don’t, then go to Troubleshooting SSR Circuitry Problems.
- Do Channels 25 thru 32 respond as programmed in the Vixen sequence?
- If they do, then goto step 29.
- Turn OFF AC power
- Swap PIC chips U10 and U7
- Turn ON AC power
- Run the Vixen sequence again
- Do Channels 1 thru 8 respond as programmed in the Vixen sequence?
- If they don't, reprogram or replace the U8 PIC chip that you moved to the U10 socket and retest
- Do Channels 25 thru 32 respond as programmed in the Vixen sequence?
- If they do, then your Renard SS24 Controller board is operational
- If they don’t, then go to Troubleshooting SSR Circuitry Problems.
- Do Channels 33 thru 40 respond as programmed in the Vixen sequence?
- If they do, then goto step 36.
- Turn OFF AC power
- Swap PIC chips U10 and U14
- Turn ON AC power
- Run the Vixen sequence again
- Do Channels 1 thru 8 respond as programmed in the Vixen sequence?
- If they don't, reprogram or replace the U8 PIC chip that you moved to the U10 socket and retest
- Do Channels 33 thru 40 respond as programmed in the Vixen sequence?
- If they do, then your Renard SS24 Controller board is operational
- If they don’t, then go to Troubleshooting SSR Circuitry Problems.
- Do Channels 41 thru 48 respond as programmed in the Vixen sequence?
- If they do, then goto step 43.
- Turn OFF AC power
- Swap PIC chips U10 and U13
- Turn ON AC power
- Run the Vixen sequence again
- Do Channels 1 thru 8 respond as programmed in the Vixen sequence?
- If they don't, reprogram or replace the U8 PIC chip that you moved to the U10 socket and retest
- Do Channels 41 thru 48 respond as programmed in the Vixen sequence?
- If they do, then your Renard SS24 Controller board is operational
- If they don’t, then go to Troubleshooting SSR Circuitry Problems.
- Do Channels 49 thru 56 respond as programmed in the Vixen sequence?
- If they do, then goto step 50.
- Turn OFF AC power
- Swap PIC chips U10 and U12
- Turn ON AC power
- Run the Vixen sequence again
- Do Channels 1 thru 8 respond as programmed in the Vixen sequence?
- If they don't, reprogram or replace the U8 PIC chip that you moved to the U10 socket and retest
- Do Channels 49 thru 56 respond as programmed in the Vixen sequence?
- If they do, then your Renard SS24 Controller board is operational
- If they don’t, then go to Troubleshooting SSR Circuitry Problems.
- Do Channels 57 thru 64 respond as programmed in the Vixen sequence?
- If they do, then goto step XX.
- Turn OFF AC power
- Swap PIC chips U10 and U11
- Turn ON AC power
- Run the Vixen sequence again
- Do Channels 1 thru 8 respond as programmed in the Vixen sequence?
- If they don't, reprogram or replace the U8 PIC chip that you moved to the U10 socket and retest
- Do Channels 57 thru 64 respond as programmed in the Vixen sequence?
- If they do, then your Renard SS24 Controller board is operational
- If they don’t, then go to Troubleshooting SSR Circuitry Problems.
Troubleshooting Power Problems
Symptom(s):
- PWR LED not lit
- IC Chips hot to the touch
- Transformer hot to the touch
Possible Problem(s):
- No Input Voltage Present
- Transformer Bad
- Transformer Wired Incorrectly
- Voltage Regulator Bad
- Voltage Regulator Polarity Wrong
- Diode Polarity Wrong
- Capacitor Polarity Wrong
- LED installed backwards
Troubleshooting Flow
The complete pdf version of this flowchart can be found here
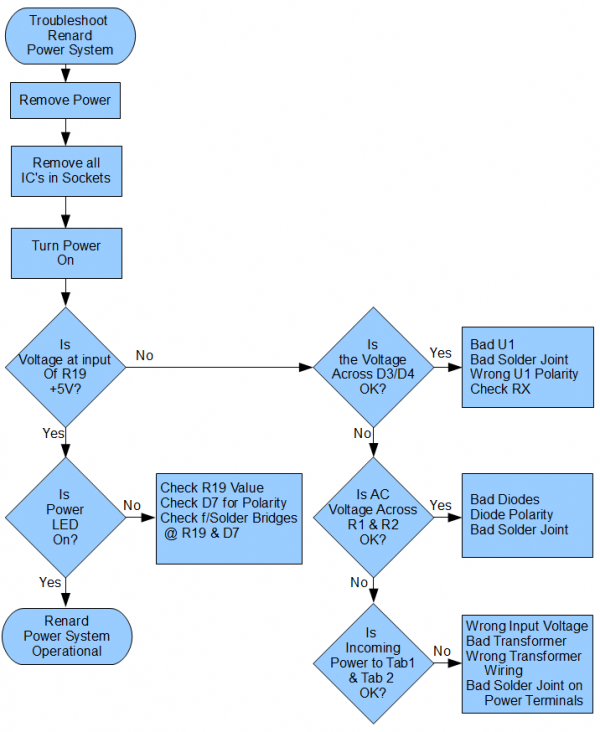
Troubleshooting Steps
- Remove power from the Renard Controller
- Disconnect all cables.
- If installed, remove all the IC chips from their sockets.
- This is to prevent them from being damaged further if you do have power problems.
- In normal use, the Renard 64XC does not require a fuse. However, since this section is about "problems", it is prudent to have one installed. The best way to do this is with an in-line fuse holder on the incoming power. Mouser PN#576-150274 (holder) and PN#576-0235.300MXP (fuse) are perfect for this. The fuse used in a 300mA fuse and is rated much smaller than the power requirements of the Renard 64XC during normal use. However, using a smaller fuse here is for safety during initial power testing. If there are any problems with bridged solder pads or a bad transformer during first power application, a small fuse will blow before any permanent damage to the SSR PCB can occur.
- Connect one SSR each to J12 and J8 with a known good CAT5 cable. Now, the link is a diagram of how to check for continuity in a cable. Here is how to use a multimeter to do just that.
- Turn ON the AC Power to the Renard Board
- Connect an AC power cable to the SSR terminal block. The 120V neutral line (wide blade on a polarized plug) goes to the N terminal and the 120V hot line goes to the 120V terminal.
- Turn ON AC power to the SSR.
- Did the SSR fuse blow?
- If it did, go to step 17(??)
- Did the in-line fuse blow?
- If it did, go to step XXXXXX.....(???)
- Measure DC voltage at U1. This is the lead closest to U4.
- Voltage should be +5 VDC +/- 0.05
- If incorrect, go to step 13(??)
- Voltage should be +5 VDC +/- 0.05
- Did the PWR LED light Up?
- If it did, go to step 21(??)
- Measure DC voltage on output side of R19. This is the end closest to the Power LED.
- If voltage is approx. 2.0-3.0 VDC, replace the LED and retest
- If voltage is approx. 5.0 VDC, then either the LED is installed backwards or it is bad
- Measure DC voltage on input side of R19. This is the end furtherest away from the Power LED.
- Voltage should be approx. 5.0 VDC.
- If correct, then double check the value of R19 and/or replace R19.
- If this is incorrect, restart the troubleshooting process.
- Voltage should be approx. 5.0 VDC.
- Measure DC voltage at the cathodes of D1 & D2.
- Voltage should be above +6 VDC but less than +12 VDC.
- If correct, voltage regulator U1 is probably bad or installed backwards.
- Voltage should be above +6 VDC but less than +12 VDC.
- Measure AC voltage between R1 and R2.
- Voltage should be above 6 VAC
- If correct, one or more diodes D1 thru D4 could be bad or incorrectly installed (backwards).
- Voltage should be above 6 VAC
- Measure AC voltage between the power terminals Tab1 & Tab2.
- Voltage should be between 6.3VAC and 7.4VAC.
- If incorrect, transformer is probably bad or wired incorrectly.
- Voltage should be between 6.3VAC and 7.4VAC.
- Measure AC voltage between the inline filter closest to the transformer and Tab1.
- Voltage should be between 6.3VAC and 7.4VAC.
- If correct, the in-line fuse is probably bad.
- Voltage should be between 6.3VAC and 7.4VAC.
- Turn OFF SSR AC power
- Remove F1 from the SSR
- Turn ON SSR AC power
- Recheck SSR AC voltage between and any N terminal.
- Voltage should be 115-120 VAC
- If the voltage is now correct but was low or missing in step 16 or blew the fuse at initial turn-on, possible problems could be:
- Bad/shorted triac
- Shorted/bad solder connection(s)
- Carefully inspect the SSR board for any possible problems with the solder connections. Fix any possible problems and then restart the troubleshooting process.
- After other attempts to fix the problem have failed, the last resort would be to remove each triac from the SSR til good power was seen with F1 installed.
- Voltage should be 115-120 VAC
- If you have gotten to this step, then your board has good +5 VDC and the PWR LED turns ON when AC power is applied without any of the IC chips installed.
- If this is incorrect, restart the troubleshooting process.
- Turn OFF AC power
- Install one of the IC chips into its respective socket.
- Turn ON AC power
- Did the PWR LED light?
- If it did not, then the last IC chip installed is bad and needs to be replaced.
- If it did, then repeat steps 22(??) thru 25(??) until all IC chips are installed.
- Your Renard board should now have all the IC chips installed and have good DC power on the board.
Troubleshooting Diagnostics Problems
Symptom(s):
- Diagnostic LEDs do not light
- HB and ZC LED do not flash
- SD LED does not come on when receiving Vixen data
- FE and/or OE LEDs light
Possible Problem(s):
- Oscillator bad
- Zero Cross signal bad
- Zero Cross Opto installed backwards
- R1/R2 are the Wrong Value
- Bad or no data coming from Vixen
- Vixen settings incorrect
- Diagnostic LEDs bad or installed backwards
- Bussed Resistor Network installed backwards
- Bussed Resistor Network is Wrong Value
- PIC bad
Troubleshooting Flow
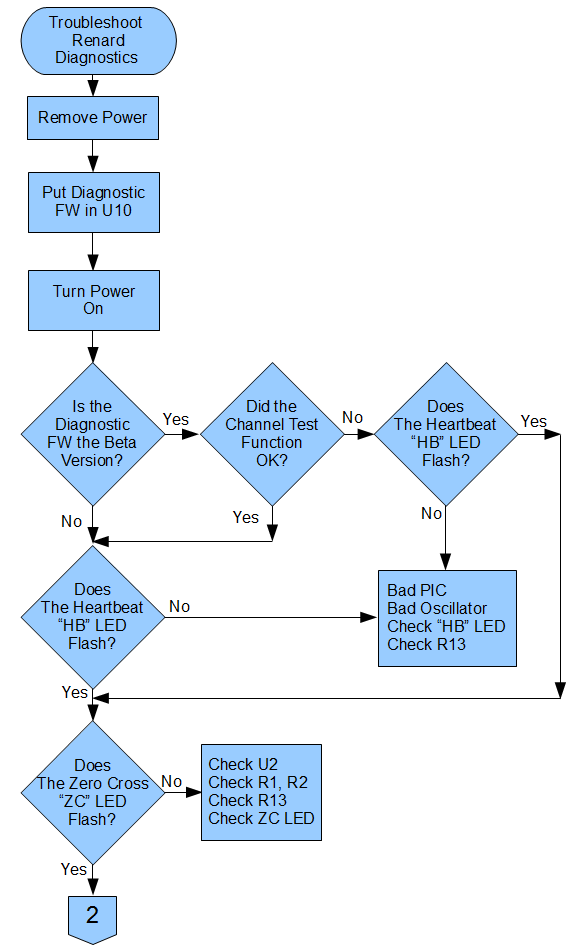
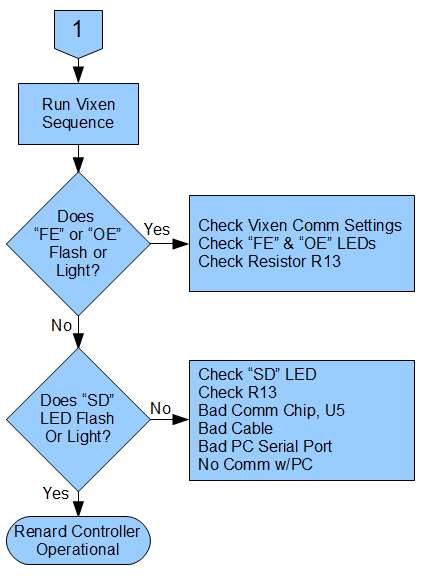
Troubleshooting Steps
- Turn OFF AC power
- Remove PIC chip U6
- Install a PIC programmed with the Beta Renard Diagnostic Firmware into the U6 position.
- Place a shunt (jumper) on JP3
- If desired, attached lights to terminal blocks [N Ch1] thru [N Ch8]. The diagnostics can be done with only the on-board LEDs.
- Ensure that the data cable from the computer running Vixen is connected to either J2 or JDP1.
- If receiving RS232 data from the computer, place a shunt on JP1.
- Do not run any Vixen sequences until directed to do so in step 19.
- Turn ON AC power
- PWR LED should be lit
- If incorrect , then go to Troubleshooting Power Problems.
- The Beta Renard Diagnostic Firmware should perform the following channel test:
- All channels ON for approx. 2 seconds
- All channels OFF for approx. 2 seconds
- Channel 1 turns ON for approx. 1 second then turns OFF
- Channel 2 (HB LED) turns ON for approx. 1 second then turns OFF
- Channel 3 turns ON for approx. 1 second then turns OFF
- Channel 4 turns ON for approx. 1 second then turns OFF
- Channel 5 (ZC LED) turns ON for approx. 1 second then turns OFF
- Channel 6 (SD LED) turns ON for approx. 1 second then turns OFF
- Channel 7 (FE LED) turns ON for approx. 1 second then turns OFF
- Channel 8 (OE LED) turns ON for approx. 1 second then turns OFF
- The above routine is done three times
- The above routine is done three times
- If no LEDs/channels came on during the above routine:
- Verify that the diagnostic LEDs are operational
- Reflash the PIC with the Beta Renard Diagnostic Firmware
- If the problem continues, then edit the Beta Renard Diagnostic Firmware to change from using the external oscillator to using the internal oscillator. If you don't know how to do this, then download this version of the Beta Renard Diagnostics Firmware.
- If the LEDs/channels are now working, then there is a problem with the oscillator U3. Check the solder pads and/or replace U3.
- If no LEDs/channels came on, then either the PIC is bad or you have no DC power to the PIC.
- If the LEDs appear dim when all are on but normal when only a single LED is lit, then it is possible that resistor network RN1 is installed backwards.
- You can choose to live with this condition but you will have to make sure that JP3 is not installed while running the operational firmware.
- If any (but not all) LEDs did not come during the step 11 routine, then go to Verifying Diagnostic LEDs
- If you used lights hooked up the channels and they did not respond correctly, then go to Troubleshooting SSR Circuitry Problems
- The Renard Diagnostic Firmware should now be blinking the HB LED (channel 2) and ZC LED (channel 5). All other channels/LEDs should be OFF.
- If the ZC LED (channel 5) is not blinking:
- Measure voltage at U6 pin 4 or U2 pin 5, should only be approximately .3 VDC. If you have an oscilloscope, you should see a signal like the purple trace in this image.
- If voltage is around 5.0 VDC , then the ZC is not working. Possible solutions:
- Replace U2
- Check the values of R1 & R2
- Check the solder pads on all the above components
- Measure voltage at U6 pin 4 or U2 pin 5, should only be approximately .3 VDC. If you have an oscilloscope, you should see a signal like the purple trace in this image.
- If you have gotten to this step, then your board appears to be functioning correctly so far. Now it is time to see if it will communicate with the computer.
REMINDER:
Make sure that Vixen is configured correctly before attempting the next step.
The settings for the Renard Dimmer Plug-In should be set as shown on
The Renard SS24 Controller Board wiki page.
- Run a Vixen sequence
NOTE:
Vixen only sends out data when there is a change in event data.
So make sure that the test sequence you are using has frequent changes in the event data..
- SD LED will be ON whenever Vixen sends data to the Renard SS24. The FE and OE LEDs should remain OFF.
- If this is correct, then your Renard SS24 has passed the diagnostics test.
- If the SD LED was ON and either or both the FE or OE LED came ON, then double check the Renard Dimmer plug-in settings in Vixen and retry.
- If no LEDs were lit in step 20, then it seems that you are not getting any data from the computer. Try the following:
- Make sure that your interconnect cable is built according to the Renard SS24 Controller wiki.
- Make sure that the Renard Dimmer plug-in is selected in Vixen.
- Replace U5
- Inspect the solder pads of U5 and the input data connector
Verifying Diagnostic LEDs
A reminder that the diagnostic LEDs referred to here are the CHANNEL LEDs associated with Channels 1-8. The Renard 64XC does not need special LEDs as they should already be installed.
- Turn OFF AC power
- Remove PIC chip U10
- Turn ON AC power
- Power LED should be lit and the DC voltage at the should be 5.0 (+/- .5) VDC.
- If incorrect , then go to Troubleshooting Power Problems
- Momentarily connect a jumper (small piece of wire) between U10 IC socket pin 13 and pin 14
- HB LED should light
- Momentarily connect a jumper between U10 IC socket pin 10 and pin 14
- ZC LED should light
- Momentarily connect a jumper between U10 IC socket pin 9 and pin 14
- SD LED should light
- Momentarily connect a jumper between U10 IC socket pin 8 and pin 14
- FE LED should light
- Momentarily connect a jumper between U10 IC socket pin 7 and pin 14
- OE LED should light
- If all the LEDs in steps 6 thru 10 did light, then the diagnostic LEDs are operational.
- If all of the LEDs in steps 6 thru 10 did not light:
- a. Check for 5.0 VDC at U6 IC socket pin 1
- If incorrect, check the solder pads and/or go back to Troubleshooting Power Problems
- b. Check for 5.0 VDC at left side of JP3
- If incorrect, check the solder pads
- c. Install shunt on JP3
- d. Check for 5.0 VDC at right side of JP3 (on underside of board).
- If incorrect, replace the shunt (jumper)
- e. Check for approx. 5.0 VDC on the pins (on underside of board) of resistor network RN1.
- If correct, then probably all the LEDs are installed backwards
- If incorrect, replace RN1
- a. Check for 5.0 VDC at U6 IC socket pin 1
- If any (but not all) of the LEDs in steps 6 thru 10 did not light, measure the DC voltage at the appropriate location on the IC socket for U10. The voltage measured at each location should be approximately 3.0-3.5 VDC.
Diagnostic LED Measure DC voltage at HB U10 IC socket pin 13 ZC U10 IC socket pin 10 SD U10 IC socket pin 9 FE U10 IC socket pin 8 OE U10 IC socket pin 7
- If any voltage measured in step 13 was 0 VDC, then most probably the associated LED is installed backwards.
- If any voltage measured in step 13 was 5 VDC, then most probably the solder pads for the associated LED are bridged.
Troubleshooting SSR Circuitry Problems
If the troubleshooting process points here, then you need to be looking at whatever external SSRs that are connected to the Renard 64XC. Basically, the functionality of the controller has been verified and the problem most likely is in the external connections or components.
The Troubleshooting Guide for the SSRez can be found here.
Symptom(s):
- Channel remains on constantly
- Channel does not come on when commanded
- Triac gate resistor burnt/blown
Possible Problem(s):
- Bad TRIAC
- TRIAC in Backwards
- Bad Opto/MOC
- Opto/MOC in Backwards
- Bad/missed Solder Joints
Troubleshooting Flow
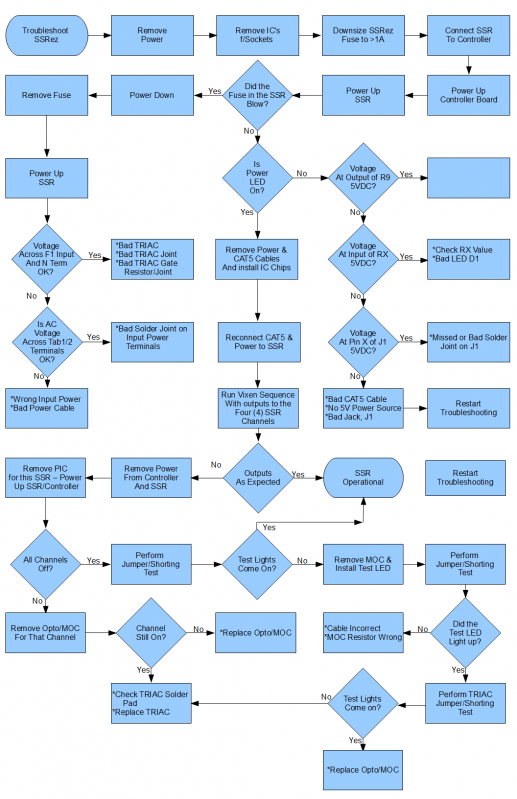
Troubleshooting Steps
- Turn OFF AC power
- Are any of the triac gate resistors (R34-R57) burnt/blown/damaged?
- If so, replace that resistor and check the solder pads on the associated triac. Blown gate resistors are usually caused by a missed solder connection on the triac.
- Are channels 13 thru 24 bad? If they are,
- Check the right side fuse
- Check the power connection to the right side of the board
- Check the solder pads on the right side fuse holder
- Is the problem in channels 1 thru 8?
- If not, go to step 21
- Remove PIC chip U6
- If installed, remove the shunt (jumper) on JP3.
- If not already installed, attach some test lights to the terminal block of the failing channel.
- Turn ON AC power
- Test lights should be OFF
- If the test lights are ON, go to step 53
- Using the following table, momentarily use a jumper to turn ON the test lights
- Test lights should come ON when the jumper is connected to the locations in the table
Channel Optoisolator Test Lights at
Terminal BlockConnect jumper between 1 M1 [N Ch1] 2 M2 [N Ch2] 3 M3 [N Ch3] 4 M4 [N Ch4] 5 M5 [N Ch5] 6 M6 [N Ch6] 7 M7 [N Ch7] 8 M8 [N Ch8]
- Does the previously bad channel now work? If it does:
- Turn OFF AC power
- Install PIC chip U6
- Begin testing again where previous failure was noted
- Turn OFF AC power
- Replace the opto (M1-M8) controlling the bad channel
- Return to step 8 and repeat tests with the new opto
- Continue here if replacing the opto did not fix the problem
- Turn OFF AC power
- Remove the opto (M1-M8) controlling the bad channel
- Turn ON AC power
SAFETY NOTICE:
In the following step you will be using a jumper wire (small piece of insulated wire) to jump
120 VAC from one pin to another. You need to be very sure that you know what pins you
are putting the jumper to before you proceed. Applying 120 VAC to the wrong
location could/can cause some very undesirable results..
- Momentarily use a jumper wire and connect between pins 4 and 6 of the opto socket
- If the lights still do not come on, it should only be one of the following things:
- Bad triac
- Bad/open triac gate resistor
- Bad solder joints on the triac, opto socket, triac gate resistor or the terminal block
- If the lights did come on, measure the voltage at the opto socket pin 1
- It should be 5 VDC
- If incorrect, check the current limiting resistor (R10-R17) associated with that opto. You should be able to read approx 5 VDC on both sides of the resistor.
- If correct, then something must have been overlooked during the troubleshooting process. Turn OFF the AC power and reinstall any removed components, then restart the troubleshooting process.
- It should be 5 VDC
- Is the problem in channels 9 thru 16?
- If not, go to step 37
- Remove PIC chip U7
- If not already installed, attach some test lights to the terminal block of the failing channel.
- Turn ON AC power
- Test lights should be OFF
- If the test lights are ON, go to step 53
- Using the following table, momentarily use a jumper to turn ON the test lights
- Test lights should come ON when the jumper is connected to the locations in the table
Channel Optoisolator Test Lights at
Terminal BlockConnect jumper between 9 M9 [N Ch9] 10 M10 [N Ch10] 11 M11 [N Ch11] 12 M12 [N Ch12] 13 M13 [N Ch13] 14 M14 [N Ch14] 15 M15 [N Ch15] 16 M16 [N Ch16]
- Does the previously bad channel now work? If it does:
- Turn OFF AC power
- Install PIC chip U7
- Begin testing again where previous failure was noted
- Turn OFF AC power
- Replace the opto (M9-M16) controlling the bad channel
- Return to step 24 and repeat tests with the new opto
- Continue here if replacing the opto did not fix the problem
- Turn OFF AC power
- Remove the opto (M9-M16) controlling the bad channel
- Turn ON AC power
SAFETY NOTICE:
In the following step you will be using a jumper wire (small piece of insulated wire) to jump
120 VAC from one pin to another. You need to be very sure that you know what pins you
are putting the jumper to before you proceed. Applying 120 VAC to the wrong
location could/can cause some very undesirable results..
- Momentarily use a jumper wire and connect between pins 4 and 6 of the opto socket
- If the lights still do not come on, it should only be one of the following things:
- Bad triac
- Bad/open triac gate resistor
- Bad solder joints on the triac, opto socket, triac gate resistor or the terminal block
- If the lights did come on, measure the voltage at the opto socket pin 1
- It should be 5 VDC
- If incorrect, check the current limiting resistor (R18-R25) associated with that opto. You should be able to read approx 5 VDC on both sides of the resistor.
- If correct, then something must have been overlooked during the troubleshooting process. Turn OFF the AC power and reinstall any removed components, then restart the troubleshooting process.
- It should be 5 VDC
- Is the problem in channels 17 thru 24?
- If not, then your Renard SS24 should be operational.
- Remove PIC chip U8
- If not already installed, attach some test lights to the terminal block of the failing channel.
- Turn ON AC power
- Test lights should be OFF
- If the test lights are ON, go to step 53
- Using the following table, momentarily use a jumper to turn ON the test lights
- Test lights should come ON when the jumper is connected to the locations in the table
Channel Optoisolator Test Lights at
Terminal BlockConnect jumper between 17 M17 [N Ch17] 18 M18 [N Ch18] 19 M19 [N Ch19] 20 M20 [N Ch20] 21 M21 [N Ch21] 22 M22 [N Ch22] 23 M23 [N Ch23] 24 M24 [N Ch24]
- Does the previously bad channel now work? If it does:
- Turn OFF AC power
- Install PIC chip U8
- Begin testing again where previous failure was noted
- Turn OFF AC power
- Replace the opto (M17-M24) controlling the bad channel
- Return to step 40 and repeat tests with the new opto
- Continue here if replacing the opto did not fix the problem
- Turn OFF AC power
- Remove the opto (M17-M24) controlling the bad channel
- Turn ON AC power
SAFETY NOTICE:
In the following step you will be using a jumper wire (small piece of insulated wire) to jump
120 VAC from one pin to another. You need to be very sure that you know what pins you
are putting the jumper to before you proceed. Applying 120 VAC to the wrong
location could/can cause some very undesirable results..
- Momentarily use a jumper wire and connect between pins 4 and 6 of the opto socket
- If the lights still do not come on, it should only be one of the following things:
- Bad triac
- Bad/open triac gate resistor
- Bad solder joints on the triac, opto socket, triac gate resistor or the terminal block
- If the lights did come on, measure the voltage at the opto socket pin 1
- It should be 5 VDC
- If incorrect, check the current limiting resistor (R26-R33) associated with that opto. You should be able to read approx 5 VDC on both sides of the resistor.
- If correct, then something must have been overlooked during the troubleshooting process. Turn OFF the AC power and reinstall any removed components, then restart the troubleshooting process.
- It should be 5 VDC
- Turn OFF AC power
- Remove the opto (M1-M24) controlling the bad channel
- Turn ON AC power
- Is the test light still ON?
- If the light is still ON then it could be either a bad triac or possibly a bridged solder joint on the triac, opto socket, triac gate resistor or the terminal block.
- If the light is OFF, then replace the opto with a new one and retest