I have 8 20x20 matrixes. I plan to use them with two Falcon differential boards, each having 4 outputs so a total of 8 outputs. Preferably, I keep the control boards and PSU in the garage but I am open to other solutions. The cables have to go out the garage door so I would like to reduce the number of cables as much as possible. Hence, I think for the data I could use my 9 conductor, solid 18AWG wire for the sprinkler system. So in the garage I somehow combine all data lines into this one calbe. Then I have a 12V power supply with some 12AWG cable and fan out the power to the 8 matrixes. Power to the differential board will come from the 12V PSU so they have the same ground as the data. Does this work? Any other suggestion? I am not quite sure yet how to fan out the 12V power out of that 12AWG cable I plan to run from the PSU.
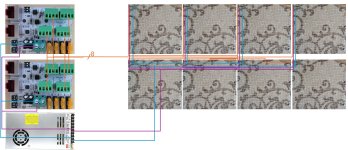
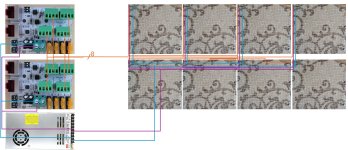